PRODUCT DEVELOPMENT
As one of the oldest and most experienced manufacturers of cast polymer products, Taylor Industries, Inc. is dedicated to creating products whose appeal extends far beyond the initial surface beauty. Each step of the manufacturing process is carefully monitored from the inspection of raw materials to the final polishing of the finished products. The true value of Taylor industries’ products, however, lies in the dedication to quality and the pride of workmanship exhibited by experienced craftsmen. The overall business philosophy is basic and simple. Produce the finest quality products available, combined with an unparalleled degree of customer service at a fair and reasonable price.
Taylor Industries was founded in 1968 by Robert Taylor, the father of the current owners, in an old knitting mill located in Linfield, PA with the initial objective of manufacturing superior quality cultured marble products. The business grew quickly and in 1972 Taylor Industries moved to the present location in Parker Ford, PA. In 1988 a major expansion to the original structure more than doubled the manufacturing capacity.
During the early years the entire cultured marble industry was plagued with tops that were cracking and crazing (spider cracking) around the drain area of the bowl. The plumbers were routinely being blamed for overtightening the drain, however Taylor Industries became suspicious when they realized that on double bowl sink tops it was always the "man's" bowl that failed. They suspected the failure was from stresses imposed in the drain area due to the hot water during shaving and cold water from brushing teeth. They designed and built a test-stand that would alternate hot and cold water into the bowl. This proved their suspicions that the cracking was caused by thermal shock and not by the plumbers. As a result, they realized that the industry needed improved resins, a primary ingredient in the manufacturing process, that could withstand the stress imposed in the drain area of a bowl. They also realized that cultured marble manufacturers must strive for improved products or all "cultured marble" would become known as a low grade product.
Robert Taylor and other concerned manufacturers banded together and formed the CMI (Cultured Marble Institute). Bob was honored to be the second president of the CMI and was instrumental in the CMI performance standard and its inclusion into the American National Standards for Plastic Lavatories, ANSI Z-124.3 The CMI influence on the resin manufacturers resulted in many new and better resin systems enabling improved thermal shock performance. Today there are numerous grades of resin systems available, however, the vast majority of cultured marble manufacturers use an inexpensive, marginal grade resin system resulting in products of questionable quality.
When the test standard was originally devised 500 cycles seemed to be a reasonable base, however, there is evidence that lavatories manufactured to marginally pass the 500 cycles industry requirement are still susceptible to thermal shock failure in the home. There is strong evidence that only lavatory basins that pass a minimum of 2,000 cycles can withstand the rigors of daily residential use. Furthermore, Taylor Industries have certified test results from independent laboratories attesting to no thermal shock failure at 3,000 cycles on all of their products.
Taylor Industries has maintained IAPMO listing and they have their products tested by independent laboratories to the ANSI Z-124.3 STANDARD, as well as, maintain active membership on the ANSI Z-124 STANDARDS COMMITTEE. They are one of the few manufacturers who have a thermal shock test-stand and continuously test their products in house to insure and maintain a very high level of quality.
By 1983 the CMI's emphasis had shifted from it's original precepts of product standards to more marketing oriented programs. For this and other major policy differences Taylor Industries decided to abandoned its association with the CMI. They began to realize that all "cultured marble" products, in general, would ultimately be perceived as a low-grade product. The introduction of solid surface products began to solve a number of the problems associated with cultured marble, but for the most part, these products were typically limited to a matte or dull finish. While impressed with certain aspects and capabilities of the typical solid surface products, they felt there remained an unfulfilled need for a high quality, durable cast polymer product with a high-luster finish.
Taylor Industries continued to strive to create a product to fulfill this need and ultimately developed a manufacturing process in combination with a selection of raw materials to create a product unique to the industry. The combination of raw materials used and the manufacturing processes employed are so vastly different from any other manufacturer and exclusive to Taylor Industries, Inc., that they registered their products with the United States Patent and Trademark Office under the trademark TERE-STONE®.
Consisting of natural stone, Dolomite (approximately 74% material composition), Terephthalic resin (approximately 24% material composition) and proprietary components (approximately 2% material composition), TERE-STONE® is cast with an "NPG" Isophthalic get coat system. While having a gel coat normally invokes a negative reaction, Taylor's gel coat system is an integral component to the base material and is resistant to stains, burns and abrasions. Scratches can be easily removed simply by buffing and polishing the surface. With a material composition and consistent color throughout the base material, similar to solid surface products, damages to the surface can be repaired utilizing a consumer-friendly patch kit.
TERE-STONE® is frequently compared to more recognized solid surface products, such as Corian and Swanstone, quartz products, such as Silestone and CaesarStone, and natural stone products, such as granite and marble. While some similarities exist with all these products, TERE-STONE® compares to none of them and is actually a stand alone product. While the color palette is comprised of shades and tones which may be similar to other products, the exclusive selection of colors known as Sierra Series™, truly distinguishes TERE-STONE® from any other product on the market, creating the look of real stone, yet more durable than granite or marble.
- Color and material coordinating products, including vanity tops, countertops, shower bases and wall panels, tub wall surrounds and decking
- Vanity Tops with integral bowls that will not crack or craze
- Shower walls with a high-luster finish that are easy to maintain and void of any grout lines
- Surface material that is resistant to chemicals, stains, cigarette burns, scorch marks and abrasions
- Standard High-Luster finish or optional Matte finish available
- Surface color and composition consistent throughout the base material
- Ten (10) Years Transferable Warranty on all vanity tops
- Unlimited design capabilities in vanity tops, countertops, shower packages, tub wall kits and decking
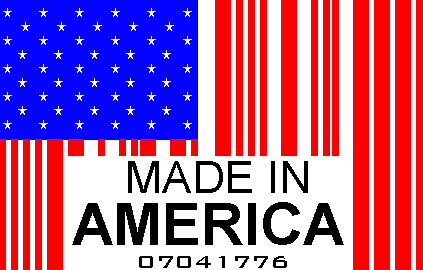